Race into
the Future!
A
CAD/CAM/CNC-Based Process
Recent
innovations in hardware and software have opened new horizons in
the way technology educators can approach the curriculum. As our world becomes increasingly more high tech, fast
paced, and competitive, many middle and high school teachers have
decided to update parts of their manual technology programs with
automated technology. One good example involves transforming the
C02 car
curriculum into a CAD/CAM/CNC based process.
The
DaVinci XYZ System
The C02 curriculum has
traditionally served as an early exposure to technology for middle
and high school students. The activity begins with students
receiving a kit with a block of wood, four wheels, two axles, and
a booklet that gives design parameters and process instructions.
Each student then studies design principles, carves a car body,
assembles the car, and races it in the school gym.
Although this activity has proved motivational and
successful, it can be improved by updating the design and
production process with CAD/CAM/CNC (computer-aided
drafting/computer-aided manufacturing/computer numerical control).
This approach teaches the skills needed in high-tech manufacturing
careers and stimulates student interest.
Benefits of CNC. Students
will work hard for something they want to own. Few at the middle
school level have the carving skills needed to produce a good
product from raw stock. Some lose interest when they see that they
can’t compete with other students who have more shop experience
or access to tools at home. Frustration arises when
expectations exceed abilities. Early failures can steer students
away from pursuing a technology career. Thus, the very mechanism
that teachers use to motivate students toward work in technology
may backfire if it produces disappointing early experiences. The use of CAD/CAM/CNC can
"level the playing field" and motivate students.
With a CNC machine
doing the carving, cars come out perfectly bilateral and even the
wildest designs can achieve the "concept car" look.
Students want these cars, and they
know that winning this activity depends more on their minds than
their hands. Fortunately, technology has advanced to a point where
students can delegate laborious manual tasks to a machine.
Producing high-quality projects no longer requires superior
dexterity. Also, if the C02 competition is a public
event, the sharp appearance of high-tech race cars will give a
good impression to parents and the public.
More than 50 middle and high
school technology education programs in south Florida have
converted to building C02 race cars with CAD/CAM/CNC,
using Techno’s IMS C02 system. With the system,
students can produce C02 metric 500 cars in less than
an hour. The cars not only satisfy Technology Student
Association (TSA) specifications, but they also have placed high
in state, regional, and national competitions. In the 1996 TSA
national competition, juniors with CAD/CAM/CNC cars placed first
and third. A highly motivated and enthusiastic special education
student took fourth place. In
the 1997 competition, four CAD/CAM/CNC-produced cars placed in the
top 10, with one taking first place.
Background: The concept of
producing C02 cars with CAD/CAM/CNC has been possible
for years, though not plausible. CAD systems could describe
complex 3-D shapes, but it took too long to get a student up to
speed to draw a car. CAM systems could generate the toolpath, but
problems arose in cutting out a car
from the top, because the cutter got buried too deep and there was
little or no side definition. Cutting from the side addressed tool
burial concerns, but it posed indexing problems.
CNC machines could cut a car, but
slow feeds and speeds made the process so time consuming that not
everyone in the class could use it. No text existed for guiding
students through all of the integrated processes.
Three companies, CNC Software (Mastercam),
Techno, and IMS Technologies have worked together to address these
challenges. The technology has come of age and pricing has fallen
to under $10,000 for a complete system. One package can
process an entire class, though some instructors add additional
software stations to allow more experimentation with design.
How the
process works:
Software
and template. The part is
designed and toolpathed, and NC-code is generated in Mastercam
integrated CAD-CAM software. The average student can quickly
design complex 3-D shapes because of a software template system
and curriculum developed by IMS Technologies.
The template is a file that resides
in the CAM software and coaches the student through the design
process. It gives the student a cross-sectional slice through the
C02 blank, every inch showing what to avoid. The
student simply draws one-half of the cross-section shape of the C02
car by charting points with the mouse. The software then creates a
spline through those points. The student changes levels, changes
depth, hides the old template, and activates the new one.
After all the cross sections are
drawn, the part is mirrored to complete the design and then
rendered. The rendered image lets the student check the design
form and determine whether it meets TSA specifications. A window
is put around the cross sections and the toolpath is generated.
The generated toolpath is for the
right side of the car. This toolpath is mirrored to produce the
left-side toolpath. Two toolpaths are necessary as the car is cut
from the right side then indexed to the left side. Precision
indexing is the key to cutting the car from the side.
The fixture. A fixture is integral to the success of
this process. Cutting the car from the side eliminates cutter
burial problems, and the fixture addresses indexing problems.
The C02 canister hole
on the blank is placed on a shaft on the back of the fixture, and
the shaft is pushed forward. The front of the blank fits in a
holder on the front of the fixture. A few taps with a soft-blow
hammer secures the blank. The car is machined on one side, then
the fixture is loosened, indexed 180, and the other side is
machined. This produces a bilaterally perfect car.
The CNC machine.
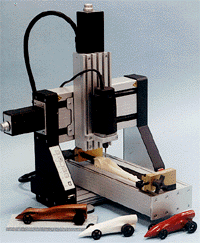
The DaVinci CNC machine works well for making C02 cars.
It has a work envelope and feedrates (140 ipm) that produce
C02 cars efficiently enough to run the whole class
through the curriculum.
The average car takes from 8 to 10 minutes per side at 80 ipm. An
average educational machine that has feedrates of 10-15 ipm would
take 80 minutes or longer. The machine has a high 24,000 rpm
spindle that machines wood well. Like industrial machines, it has
ball screws on all three axes, which increases power and accuracy.
The curriculum. The IMS C02 curriculum
integrates all aspects of the procedure from machine and fixture
setup to software instructions. Students and teachers receive
instructional training videos and curriculum guides, step-by-step
instructions for assemble and use, clamps, fixtures, and software.
The basic system includes CAD software. CAM toolpath generation
software, and a CNC machine.
The CAM software eliminates hand
carving by creating tooling instructions for the CNC machine,
based on the CAD drawing specifications. The three-axis CNC machine
performs the manual labor with precision, speed, and reliability.
The only manual work left for students is finishing touches, such
as light sanding, painting the car, and adding wheels. This
approach saves students time and lets them focus on learning new
skills and experimentation.
The speed of the CNC machine
also allows students to produce more than one race car,
experimenting with different materials and designs and testing
aerodynamic differences. This freedom to experiment encourages
innovative thinking, creative problem solving, and collaborative
brainstorming efforts. This activity results in students
learning transferable skills by using the same prototype and
design software and machines found in high-tech industrial
workplaces. Students also
benefit from having the luxury of performing trial-and-error
learning and discovery.
Other options. Advanced secondary students can go beyond
defining their cars with simple cross-sectional slices. Cars can
be designed using full surface modeling, which allows for greater
detail and more variation in shape.
Students might also
take on the engineering challenge of designing a car/boat/plane
body. Here, they would take into consideration the particular
requirements of each type of vehicle:
Car – The most
critical design factor here is weight, then aerodynamic shape,
then friction and alignment of mechanical parts, wheels, and
axles. Points would be awarded for speed.
Boat – The
first consideration is hydrodynamic shape (water flow), then the
amount of water the shape displaces, then the placement of the
mast. The boat competition would use the same C02 body,
with a spent C02 cartridge as ballast. A mast hole
would be drilled into the bottom of the car to hold a standard
sail. The race would take place in a vinyl rain gutter filled with
water, and the student would provide power with air from a
portable fan. Points would be awarded for speed and straightness
of course.
Plane – The
critical design factor is placement of the wings at the center
gravity, then trimming of the tail, body shape, and fuselage. The
C02 cartridge would be removed for this competition and
a special plug, with tail fin support and adjustment mechanism,
would be placed in the hole. The body would be slotted to accept
prefabricated wings. The wings would slide forward and back to
adjust for center of gravity. Competition would use a mechanical
launcher and points would be awarded for straightness of flight
and distance.
|